Thanks Pieter,
A small update now. I'm doing lots of work on her, but you hardly see it. During my last deployment I didn't get to make anything, but I made a page with scetches of the larger parts that I still had to make. I wrote all measurements next to it as well, so I don't really have to remeasure. This allows me to work much faster than before as I always went back and forth between computer for pictures and plans to measure and then back again and so on. Now I just have that page and I can continue cutting parts and assembling them.
Since I got ahead of schedule on those parts I also continue on the build itself. With the deck house in place I could finally continue on the missing midship part of the pipe rack. It's proving to be a real head breaker as some parts are hard to see on any picture and I have to start from the deck up.
So for now I've added the sea water overboard line from the cargo heater (not in place yet) to the deckhouse. I'm busy on the supports for that line. At the same time I'm also putting the first part of the big sea water supply line from engine room to the deck. That's the first big line that will be placed on the piperack since it's also the most outboard one. In this dry fit you can also see the biggest diameter line, the Inert Gas line, just to fit.
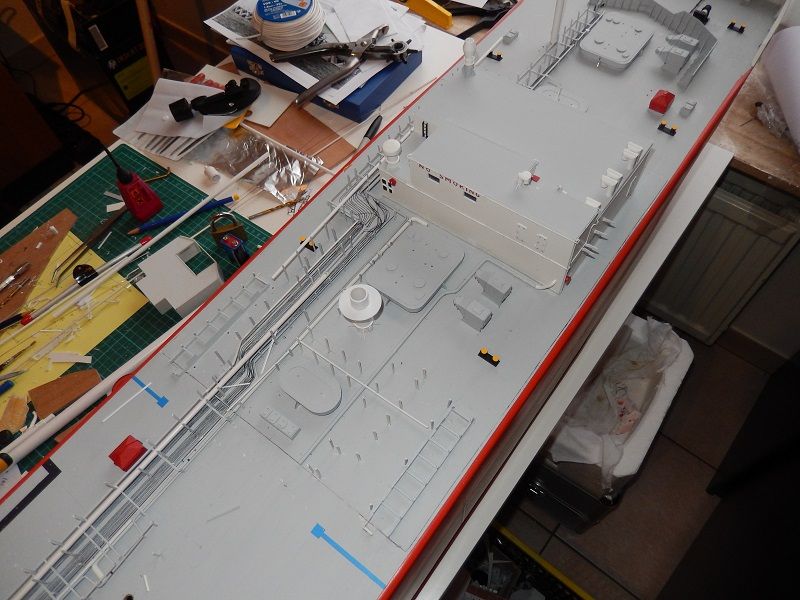
This is the reason why the deck house first had to be placed, so parts of the piperack are connected to it.
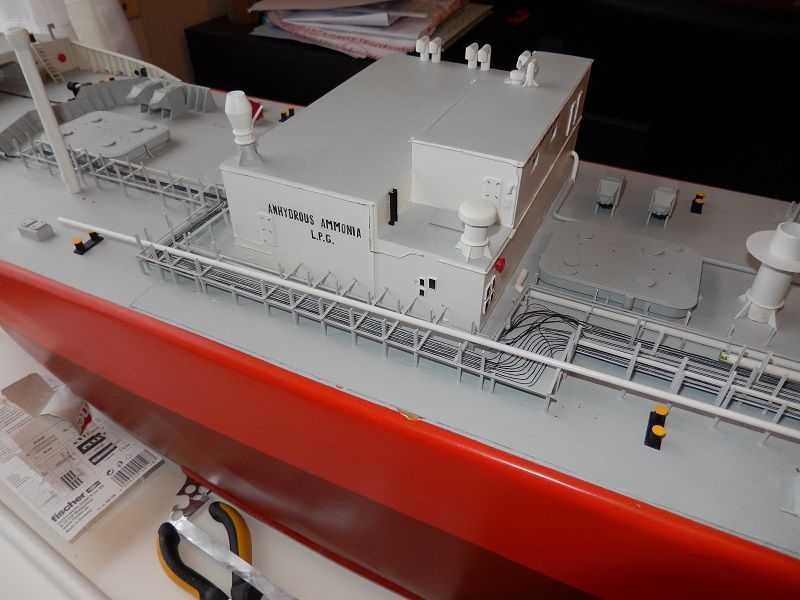
Here is the first fit of some of the large pipes. All styrene tubing. I can go two directions now, either finish part of the aft piperack, with all piping to the aft tank etc in place up till the midship hatch. Or I can continue line by line all the way forward. Not sure which direction to take yet.
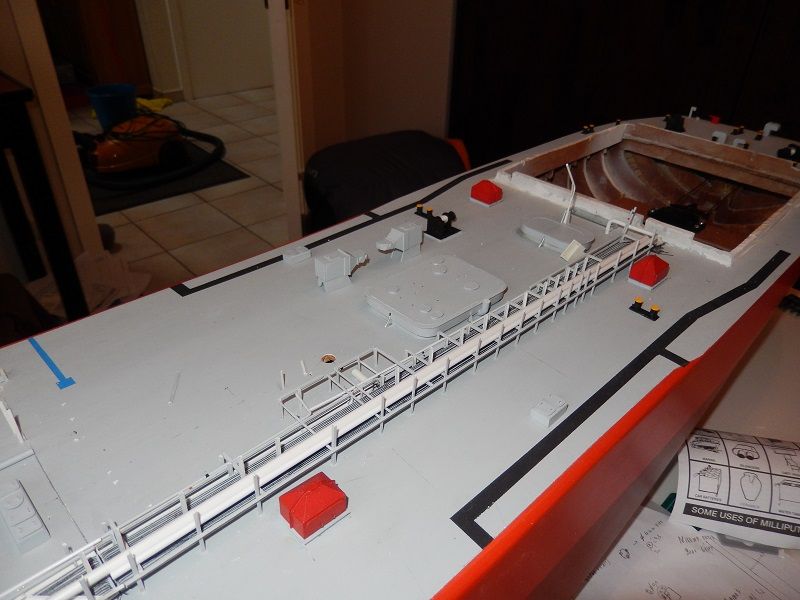
For all the bends in the piping I have different solutions. For anything up to 1.5mm styrene tubing, I can bend them by hand without any major deformation.
For 2mm I'll insert a brass wire. For 2.5mm I have some electrical construction wire, a copper wire which is jacketed by a sort of rubber, I bought the white version. This is made for bending, so it actually works nice! Just have to make my bends and then glue it to the styrene tubes.
For 3mm I use the 1.5mm copper core from the above wire and insert it in the tube itself. Because the tube is then filled entirely by something incompressible, it bends nicely till 90° without major deformation.
4mm, I still have to test, I guess I'll try again the copper core method, otherwise perhaps I'll insert the complete electrical wire (2.5mm).
This way I'm avoiding the boiling water method etc. since that would be very tedious due to the high amount of turns and all the fitting issues on the ship itself.
The only issue I haven't resolved for now is a method to make cooling vanes for the different cargo pump electro motors. I've tried to make a mini "accordeon" ^^^^ shape from alu foil. It actually worked, but it's still slightly too high and very difficult to fit. I've been thinking about small pieces of wire, like Jaguar did for his 1/200 motors, but that won't look too good either... Any tips for that are welcome.